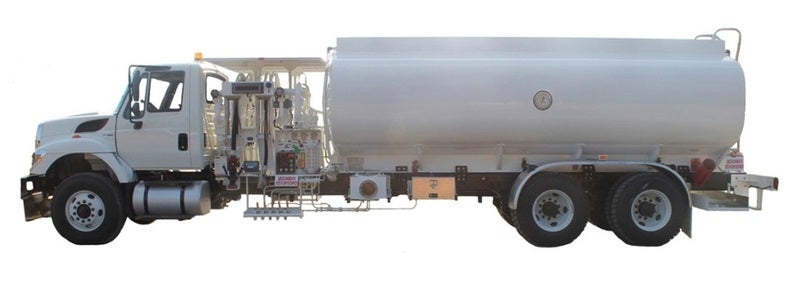
BETA supplies the commercial airline industry, major oil companies and US and foreign allied militaries with safe and reliable refuelling equipment.
The company provides aviation / aircraft refuellers, hydrant dispensers and carts, refuelling modules and trucks, aluminium vessels and filtration systems, as well as mobile and emergency fuelling solutions.
Hydrant carts for the aviation industry
BETA’s wide-body and stationary hydrant carts optimise fuelling operations some of the highest dispensing flow rates in the industry.
The modular design elements are shared with other hydrant designs to lower fleet maintenance costs.
These carts fuel an entire range of aircraft while also providing quicker gate turns with fewer operators, no chassis maintenance required, and less aircraft damage.
Features include:
- Self-propelled cart able to serve multiple gates
- Hydrostatic drive to minimise maintenance and emissions when compared with hydrant dispensing trucks
- Stainless-steel tubing for fuel sensing line, offering greater durability compared with synflex
- Robust boom design minimises leaks and hose replacements associated with jack risers. This also reduces stress on under-wing nozzles and aircraft fuelling manifolds
- Corrosion-resistant aluminium filtration, eliminating maintenance of internal epoxy coating
- On-board diagnostics and troubleshooting capability with wireless, remote support
- Non-proprietary components so replacement parts can be quickly delivered, maximising uptime and fuel efficiency
- Built on a proven design from more than 30 years of military and commercial applications
- Made from corrosion-resistant aluminium and stainless-steel to increase service life and reduce maintenance costs
Refuelling Trucks
BETA’s refuelling trucks use advanced technology to help our customers minimise costs, boost operator support, and optimise fleet management. This is accomplished through reducing installation time and maintenance by eliminating terminal boxes and plug-in wiring.
All trucks feature automated electronic controls and multi-function touchscreen displays to decrease operator errors and fuelling time. The modular design enables lower lifetime cost by reusing the fuelling system on a new chassis.
The refuelling trucks also feature automatic on-board diagnostics and troubleshooting alerts, along with automatically generated fuel and safety data reports.
BETA manufactures the following equipment and variations:
- 10kl, 7kl, 5kl, 40kl, 30kl, 20kl, and custom aviation Jet A-1 refuellers
- 500gal, 750gal, 1,000gal, 1,200gal, 2kl, 1kl, 5kl AVGAS refuellers
- Ramp servers
Aluminium vessels and filtration
BETA is an American Society of Steel Engineers (ASME) U-Stamped certified manufacturing facility approved to manufacture and validate filtration vessels for global aviation.
Aluminium and stainless-steel vessels eliminate the risk of internal epoxy damage that commonly occurs in carbon steel vessels.
BETA is the only commercial aviation refuelling vehicle manufacturer certified to develop code-stamped vessels, and carries additional certifications, including R-Stamp for refurbishment and repair in-house or in-field.
The company offers a full range of designs and performance requirements to ensure fuel is clean and dry.
Modules for hydrant dispensers and refuellers
BETA manufactures aviation refuellers and hydrant dispensers modules, which are designed for turnkey integration and are capable of flow rates of up to 600 gallons per minute (GPM) or 2,300 litres per minute (LPM) for modules, and 1,000GPM or 3,800 LPM for dispenser modules.
Advantages of BETA modules include:
- Automated electronic controls and diagnostics for operational efficiency
- Fuelling and safety data reports to help optimise fleet management
- Complete drop-in system
- Pumping systems to maximise flow rate, and reduce maintenance and fuel costs
Parts and components for refuelling systems
BETA supports its field equipment by stocking necessary parts and components.
By manufacturing more than 70% of the components on the equipment provided, they become available to customers.
The full range of consumable parts varies from filter elements and placards to hose couplers.
Mobile fuelling solutions
BETA provides a variety of fuel delivery solutions for on-site, mobile fuelling fleets, repair centres and tank truck builders.
BETA is the sole distributor of Alfons Haar’s complete range of fuel transport equipment in North and South America. Alfons Haar pumps have been optimised over decades in stationary applications, tank trucks, heating oil delivery and aircraft fuelling.
The company has also partnered with repair centres and tank truck builders nationwide to provide authorised Alfons Haar service centres (ASC). Together with its ASC, BETA can provide a client’s fleet with the most innovative equipment in the industry.
About BETA Refueling Systems
BETA has thousands of aviation refuelling units in service today, in more than 30 countries around the world. It also has the highest dispensing flow rates in the industry by manufacturing and quality controlling more than 70% of the content on its equipment.
Each product undergoes a rigorous quality inspection process throughout manufacturing, before full pre-commission in BETA’s new state-of-the-art flow testing lab, simulating real world fuelling scenarios, failure modes, and corrective actions required to ensure maximum operational uptime.
BETA’s engineering team is experienced in designing fuelling systems for operational simplicity and long-term reliability. Every operational metric at BETA is focused on improving product reliability, providing fanatical support, and meeting or exceeding delivery commitments.
The company employs LEAN Manufacturing tools to eliminate waste and deliver value to our customers. Its development process engages with customers throughout every build, focuses on their operational needs, and supports them long after its product leaves the factory.
BETA’s commitment to Reliability, Support, and Delivery™ starts with its dedication to employees and their safety, and follows through the engineering, manufacturing, and quality assurance process
Driven by comprehensive health, safety, and environmental programmes, BETA makes every effort to ensure the continuous safety of its employees.
The company is committed to meeting its customers’ most critical needs. Starting from engineering to fabrication, and final assembly to green-tag validation, every person and process in BETA is measured and held accountable to three critical factors, product reliability, technical support and punctual delivery.