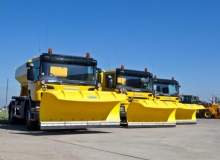
Airports and airlines start making plans for the following winter season almost as soon as the current one has passed. With particular disruption experienced in Europe in December 2010 and freezing temperatures expected in 2011 across Europe and North America Frances Cook reports on how airports and airlines have been investing in equipment, de-icing products and strategies that will improve flight operations and passengers’ experiences during the 2011 to 2012 winter period.
UK’s Birmingham Airport spotlight
Last December temperatures on the airfield at Birmingham Airport – the UK’s seventh busiest airport – reached -18°C and out of the 16 hours that the airport had to close, eight of these were during core hours, between 6am and 10pm. Challenges on the ramp and with some of the de-icing products were brought up during the winter review, and changes will take effect as a result this coming winter.
"This year, the airport is providing even greater focus on clearance around the ramp," said Rob Cooke, Birmingham Airport’s Head of Aerodrome Operations.
"It will also be deploying two new John Deere Tractors along with a ‘MultiHog’ combination brush / de-icer designed to get into very tight spaces around aircraft stand equipment." The airport is also increasing its de-icer storage capacity again and now has two new pavement de-icing rigs on-line. A new 20ft wide ramp plough will also be deployed.
While the airport now has nearly 30 pieces of snow and ice clearing equipment – many of which are due to a £1.5 million investment over the last five years – one of the biggest challenges remains how to plan around weather forecasts.
"Predicting accurately weather conditions for the forthcoming winter season is always difficult because forecast accuracy diminishes with time, and although we will get general predictions they’re not reliable enough to base resource planning around," said Cooke.
How well do you really know your competitors?
Access the most comprehensive Company Profiles on the market, powered by GlobalData. Save hours of research. Gain competitive edge.
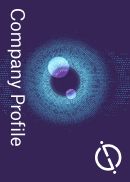
Thank you!
Your download email will arrive shortly
Not ready to buy yet? Download a free sample
We are confident about the unique quality of our Company Profiles. However, we want you to make the most beneficial decision for your business, so we offer a free sample that you can download by submitting the below form
By GlobalDataHeathrow’s lessons learned from experience
The potential impact of the weather was not anticipated effectively at Heathrow, Europe’s busiest airport, last winter and major disruptions occurred in late December 2010.
The combination of a low state of preparedness ahead of the snow and insufficient stock of critical supplies made coping with the freezing conditions and snow fall rate problematic. Cancelled flights and communication problems meant approximately 9,500 passengers spent the night in Heathrow terminals on one night.
In March 2011 an inquiry made 14 recommendations on how the airport could improve its resilience. These included restructuring the crisis management process, enhancing airport and passenger communications and changing how the snowfall and de-icing process is dealt with.
To facilitate the effectiveness of this review process, the inquiry team looked at 13 airports that operate in extreme winter weather and snow. These included Chicago, Denver, Toronto, Frankfurt, Montreal, Stockholm and Ottawa.
While the level of snow Heathrow received was not rare at 9cm, the rate was unprecedented. Approximately 7cm fell in one hour on 18th December – 10cm of snowfall is the equivalent of 60,000 tons or the weight of 345 unloaded Boeing 747 jumbo jets – which is rare and had not occurred at the airport since hourly records began in 2005.
Where to put this amount of snow became a major issue for the airport (especially when mixed with de-icer as then it has to be disposed of carefully through the airport’s pollution control system).
For 2011 and 2012, short-term storage will be made available on the airfield and once filled the snow will be transported to Heathrow property offsite. To improve this process an additional 72 snow clearing vehicles have been purchased – bringing the number to 185 -and just more than £11 million has been spent on snow equipment.
The lack of de-icing product in stock also affected operations. On 16th December the airport had 206,810 litres product (glycol) available and 105,960 on order. However, due to the weather it was using about 75,000 litres a day and by 19th December had only 129,770 available – plus the supply was affected by distribution problems.
For 2011 both stocks and storage will be increased. New tanks holding one million litres will be installed on the airfield and increased storage capacity for runway de-icer is also being introduced.
Lufthansa services at Stuttgart
Stuttgart serves approximately ten million passengers each year and for many decades Lufthansa Technik has provided its de-icing services. The company operates a fleet of 13 de-icing trucks to handle more than 1,300 aircraft departures each week. "Our expertise ensures that Stuttgart airport doesn’t ever close down for lack of aicraft de-icing," said a Lufthansa Technik spokesman.
Once an aircraft reaches a de-icing position, two Lufthansa de-icing trucks approach the aircraft from both sides. Heated de-icing fluid is sprayed onto the aircraft – starting from the inside of the aircraft body along the wing to the wing tip – removing all frozen contaminants. Once the front wing is finished the trucks do the same for the back and the stabilisers.
"The operators hardly take five to seven minutes to protect even a large aircraft," said a Lufthansa Technik spokesman. "We have been using trucks by the manufacturer Vestergaard from Denmark. Other manufacturers include Safeaero and Kiitokori from Europe as well as JBT and Global from the US." To improve upon its process further, the company will be purchasing six new de-icing trucks by 2012.
Halifax Stanfield introduces multifunctional equipment
Halifax Stanfield International Airport (HISA) on Canada’s east coast received approximately 3.5 million passengers in 2010, and with winters that can reach -20°C, the airport improves its winter resilience operations each year.
In 2007 the use of urea, a naturally-occurring chemical used to melt the ice, was ceased in favour of a more environmentally-friendly product, sodium formate, and then potassium acetate was introduced to further improve the effectiveness of the new process.
"While the solid product worked well alone, it is light enough to be driven away from the surfaces to be melted by winds," said Clayton Maynard, Manager of Airside Services, Halifax International Airport Authority. "The dry solid product is now pre-wet with the liquid which helps the solid product ‘stick’ to the frozen surfaces."
The airport has introduced multifunctional equipment to remove snow and equipment that is faster and more effective at removing snow than its existing mechanical range. "Part of the aged fleet of plow trucks with tow behind sweeper / blowers have been replaced already and their effectiveness proven with the remainder of the fleet to be replaced before the beginning of this snow season," said Maynard.
He added: "New efficient computer controlled anti and de-ice chemical dispersal equipment should decrease the amount of time while spreading the exact amount of chemicals needed on the field in a more efficient manner."