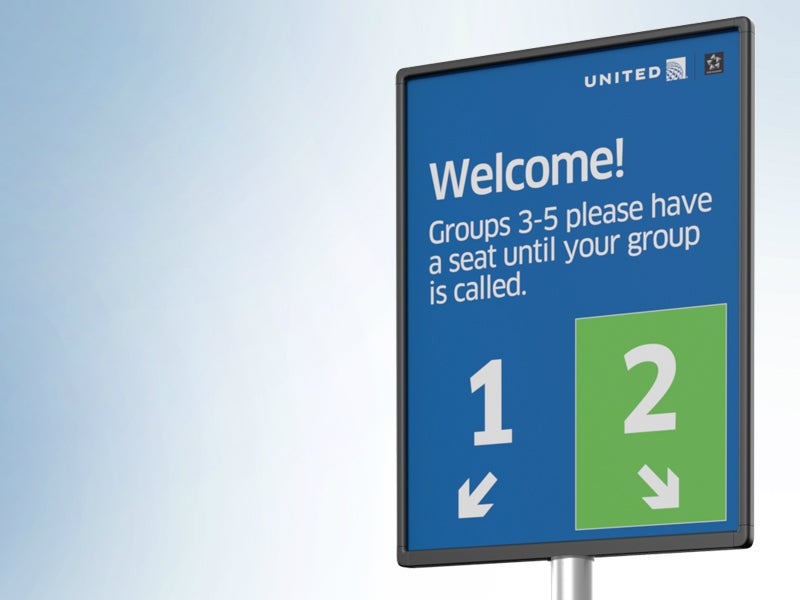
Dependability. Reliability. Responsiveness.
Multinational corporations such as United Airlines demand these attributes from their business partners, and they received exactly that from Visiontron.
United was undertaking a years-long initiative called Better Boarding. The goal was to help its customers and gate agents navigate the boarding process more quickly and comfortably. Although it may seem simple, the subtle complexities of the boarding process have vexed travelers and airlines for decades. United wanted to finally get the boarding process right, and was spending millions of dollars to do so.
To help make its expansive (and expensive) vision a reality, United engaged its longtime business partner Visiontron. The family owned company has been involved in the aviation industry since the 1960s, when it developed the very first mechanical arrival and departure boards for airports. Today, its RETRACTA-BELT® stanchions, baggage sizers, post and panel systems, signage, and many more products are the airline industry standard for what some call ‘crowd control’ but Visiontron calls ‘people guidance’. It’s the standard in numerous other industries as well. The majority of its products are designed, manufactured and serviced in the US, in fact, under one roof on Long Island, New York.
United executives and Visiontron engineers worked closely together through many trial iterations of the Better Boarding project. Visiontron would design, manufacture and prototype custom products to United’s spec, often from scratch, to precisely suit the airline’s needs. In some cases, Visiontron would collaboratively improve on United’s ideas, letting the company know about possibilities United might not have been aware of.
Throughout the process, Visiontron was always ready and able to adjust at United’s request. The fact that Visiontron’s unparalleled rapid-response customer service department is housed in the same building as its engineering, design and operations teams ensured that the right people were always tuned into the project in real time, 24/7/365.
In September 2018, United formally introduced Better Boarding worldwide, featuring Visiontron’s thoughtfully engineered 6ft tall signpost and RETRACTA-BELT® stanchions. Almost as important as the products themselves was Visiontron’s expert management of the logistics involved with the global roll-out. Visiontron’s deep knowledge of domestic and international shipping modes and various customs hurdles around the world was vital to the successful implementation of the program.
United, like many other customers large and small over the years, was very appreciative of Visiontron’s execution and was pleased that Visiontron consistently fulfilled their needs. Because of the wide, global scope of the project, United had initially considered using multiple vendors. But Visiontron quickly proved to the airline that it could handle the entire load by itself.
“We’re not just a manufacturer,” said Visiontron vice-president and chief engineer Bryan Torsiello. “We work closely with our customers, and they trust us to develop solutions from their ideas. We’re always working as their partner from start to finish, from concept to roll-out. We test, we knock ideas around, we come back to the table and improve on things. That’s just how Visiontron operates.”