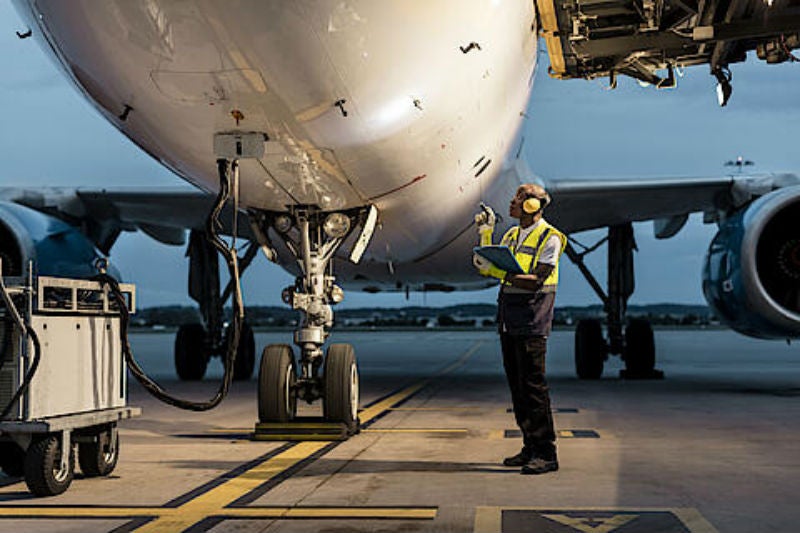
The line maintenance services industry is undergoing major growth and transformation due to increased air travel.
Line maintenance service providers, organisations and teams must contend with a host of challenges from workforce shortages and increased competition to regulatory demands and a lack of common data standards.
There are also major challenges relating to staff scheduling and communications. Optimisation software, particularly when applied in the line maintenance area, is proving an effective tool in helping line maintenance teams mitigate the challenges and stay ahead of market developments.
Line maintenance challenges
Aircraft line maintenance is typically performed during an aircraft’s turnaround period. In some situations, the line maintenance tasks may extend beyond the turnaround period such as in the case of MROs that also manage aircraft towing to hangars and/or basic maintenance checks during an aircraft’s longer night stops.
Most line maintenance is characterised by the 50% factor. That is, 50% of the work is either unplanned or will be performed at times different from those planned. To accommodate tight flight schedules and avoid maintenance delays, there are decisions that must be made on the fly to reassign staff to address unplanned issues promptly.
When these decisions are made manually, it is not atypical for subpar decisions to be made, resulting in lower staff productivity and unnecessary technical delays. Given that aircraft line maintenance is directly linked to flight schedules, it is clear why line maintenance workers largely base their work patterns based on these schedules.
That said, considering that flights are sometimes on-schedule and sometimes late, it is necessary for line maintenance workers to be prepared for potential schedule changes. While certain tasks can be planned upfront, many other tasks are contingent based on various factors. Therefore, line maintenance workers are never completely sure when to expect an aircraft until it is on the ground.
Communication and transparency of shared information between departments (i.e., line maintenance, maintenance control center, flight operations and cockpit crew) is another area that presents challenges to the line maintenance operations. When communication or information sharing is not optimised, questions arise as to whether all stakeholders are looking at the same data and schedule, and/or whether they have the same forecasts for when an aircraft’s maintenance work will be completed.
It is important that they all have access to the same situational view so that the best decisions can be made and communicated to all parties. Since communications can be conducted via phone, radio and screens, it is critical that there be a transparent flow of information so that inefficiencies can be quickly identified and addressed. Staff scheduling in line maintenance also requires processes to be at peak efficiency.
Six to twelve month in advance, line maintenance planners must be able to project the workload on given days, along with what workforce skills will be required. Through accurate forecasts, the planners can create shift plans that will best cover the expected workload.
These forecasts, while difficult to create, are essential when preparing for fleet changes, schedule changes, or changes in the staff’s skill set. As the day of operations approaches, staff schedulers must reassess upcoming maintenance workload and review their shift plan.
Since each aircraft has a small number of items that require repair, but which are not critical for flight safety, they need only be repaired prior to a certain time. The list containing these various open items is in constant flux along with the expiration dates for each items repair. This prompts the potential need for extra staff on short notice.
This situation, coupled with each staff member’s personal requests for days off, shift swaps and/or planned vacations or leaves, further creates internal discord. Once line maintenance operations commences, there are challenges relating to the designated staff with the right qualification calling in sick and requiring a new staff assignment, aircraft requiring unexpected repairs, and the usual irregularities that can occur during the day’s operations.
Advancing line maintenance with optimisation software
Optimisation software, such as INFORM’s Line Maintenance Solution, effectively addresses these primary challenges facing line maintenance operations. Regarding staff schedules, there are solutions that cover all related processes and facilitate advanced planning.
Specifically, these solutions support long-term planning of line maintenance staff. Applying rule-based functions, they estimate the line maintenance workload based on the number of flights to be covered. Relying on a sound workload estimate, optimal shift plans can be generated to ensure the efficient work coverage.
Additionally, these tools are effective for evaluating multiple scenarios such as higher or lower workload impacts, as well as, how the introduction of new aircraft into a fleet or the effect of changing labor agreements will impact the expected workload.
Once the need for shifts and skills have been addressed, optimisation software also supports workforce scheduling and rostering by generating optimum staff rosters that accurately reflect each staff member’s skills, time-off/vacation wishes, and other employee requests or schedule constraints.
Using the solution’s web-based employee portal, each staff member can view and manage their own schedule online on a 24/7 basis giving them a sense of control over their schedules. Staff management during the day of operations is also greatly enhanced by sophisticated line maintenance solutions. When flight irregularities occur and unexpected maintenance requirements are reported, the solution facilitates a quick and optimised response to reduce technical delays and increase overall staff productivity.
Because of the solution’s mobile platform, tasks can be tracked individually and addressed promptly. Through this structured communication and information gathering, the analysis of key performance indicators becomes much easier and effective in driving continuous improvement.