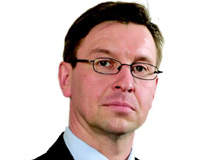
Much effort has gone into improving Helsinki-Vantaa airport and its services over the past 15 years, including the opening of a third runway in 2002, and €10m worth of extended and newly built aprons. Operating conditions in winter are extremely challenging, with temperatures well below zero, but Esa Siponen’s team are always ready thanks to meticulous preparation.
How far in advance do you have to prepare for the winter season?
This year our preparations started in May, and that’s normal for us. In our workshop we take great care to properly maintain all of our winter equipment and machines. There are just so many of them and they are all mission critical, so it would be a mistake to lock them away for a long period and just forget about them. During summertime we make the effort to maintain our machines the way they should be, so we have about five months to make sure everything will be running smoothly when the winter season comes around.
It’s quite typical for this region to prepare so far in advance. Last year the winter period was unusually easy for us, though. Managing our fleet required only about 750 working hours per machine last winter. The year before it was almost 900. In autumn it is normal to go through a round of meetings with the airlines at the tower and also the crowd-handling companies because we have to plan ahead for any changes.
In September our seasonal workers return to the airport. Many of them come year after year and are trained by our permanent employees, so it’s very much a learning period for them. Last year we had 50 seasonal workers with a permanent staff of about 60, so it’s roughly half and half in winter. That should give you an idea of how much more intensive and demanding the work can be over the winter months.
September is our practising and training month. I believe that with our permanent staff doing the training, it’s the best practice and instruction anybody could receive. They run through the safety rules, operating and manoeuvring procedures, and cleaning. Of course, in five or six months we have to start the whole process all over again.
How well do you really know your competitors?
Access the most comprehensive Company Profiles on the market, powered by GlobalData. Save hours of research. Gain competitive edge.
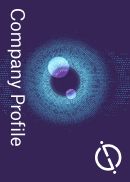
Thank you!
Your download email will arrive shortly
Not ready to buy yet? Download a free sample
We are confident about the unique quality of our Company Profiles. However, we want you to make the most beneficial decision for your business, so we offer a free sample that you can download by submitting the below form
By GlobalDataSo do weather conditions vary drastically between the seasons, and is your job becoming more unpredictable with changes in climate?
The summer and winter seasons demand two totally different types of work. In fact, the contrast could not be starker. During the summer season, maintenance work in particular is very different. In a typical day we will spend time fixing any damages and cutting grass. There are often some bird problems that we don’t have during winter. In the winter season, though, the main focus is on how we handle immediate problems associated with the weather conditions.
Our biggest practice event is usually 1 September. After that we will specify orders and work out how we can do things better next time around. Every time we experience a blizzard we have the same system for reviewing our processes, setting up meetings and establishing how exactly we can improve.
You have to remember that blizzards and snowfalls are very common for us. We’ve had sensors on the runways for around ten years now and our weather prediction systems are more than adequate, so we have good information on projected changes in the weather. We will usually know the situation two to four hours ahead.
When we know snow is coming we can call in extra employees from home. Normally during winter (from November to April) we have people on call 24 hours through seven days. So we have around 15 employees, but when snowfall is predicted we will double the number of employees and call in our contractors to begin work immediately. That way we are always prepared.
Who else is involved in running ground operations during the winter season? Do you have any partners or contracts with outside firms?
We work with a number of businesses from the outside including a Finnish company called Viselje, which monitors the runways for us. For weather forecasting we use a service provider owned by the Finnish Government. We have many other contractors here on site, mainly apron-side.
Why do we do this? Perhaps the effort involved in removing snow offers a good explanation. When you have normal snowfall, say around 10cm of snow, cleaning it all up can take about one week. But after heavy snowfall it can take around two weeks. So we have to carry extra snow away, clean the signs and clean the ILS system areas. It’s a mammoth task.
How do you manage the de-icing process, and what technical challenges are involved in this?
For the de-icing of the runways, our approach is based very much on preventative methods. We look at the condensation point and make sure that we optimise the process of spreading the additives. There are environmental issues, which are quite important, and safety remains our number one priority at all times.
But the chemicals involved are quite expensive, so that also enters our thinking. Last year we used about ten million litres of de-icer. Timing is the critical factor when we are spreading the de-icing liquid.
If extensive icing has already occurred it takes so much more time to sort out after the fact, and of course we can’t use the runways while the aftercare is taking place.
Using chemical additives also creates some technical difficulties. De-icing liquids can be very disruptive when they come into contact with electrical connectors, whether that is in lighting systems or winter service equipment, and these electrical problems are quite notorious in the industry.
Therefore, like anybody else, we have to do lots of preventative maintenance work with electric parts and components, and we carry out regular checks.
So what happens when things do go wrong?
Naturally, when it’s snowing our machines will occasionally go wrong, so we need our workshop to be fully operational and ready 24/7 for any new problems.
The last time that we had bad technical problems here was around December 2004, in the middle of unusually extreme weather conditions. In all, we were only closed for about three hours. And since then we’ve had no major problems at all. You have to remember that what is normal snowfall for us might be considered a blizzard in Central Europe.
We have a direct line to the meteorological office so we can get the best possible forecast. However, what is key to our operations is not incredibly high-tech equipment, but the fact that we have lots of telephone communication with the ATC tower and the airline operating centres. The main thing is strong cooperation between all the different parties involved in running the airport, including the ground handling companies and maintenance units.
When I joined Finavia I was really impressed by how the airport worked. All the divisions and units are closely entwined. Everything has some connection to the airlines. Everything we do involves cooperation with the companies and our local partners. The winter operation is all about cooperation, really – it’s the name of the game at Helsinki-Vantaa airport.