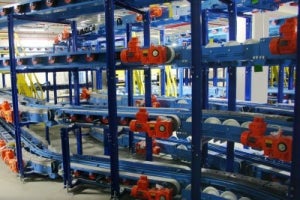
Frankfurt Airport is expecting a steep rise in the volume of both freight and passenger traffic. The new northwest runway has just become operational, a new terminal is in the planning stage, and in autumn 2012 the new A-Plus pier will be opened – increasing the number of A380 megaliners that can be processed simultaneously. In order to keep luggage loading time under 45 minutes even in the face of more air traffic and tightened security measures, efficient and highly reliable handling technology is required. The extensive baggage handling system at the new pier, supplied by the BEUMER Group, is driven by geared motors from NORD DRIVESYSTEMS.
A380s offer more seating and cargo space than any other commercial aircraft and they perfectly suit long-distance flights. They will therefore be the transport method of choice in the future. Airports with the necessary infrastructure in place will clearly hold the advantage.
Fast baggage handling facility for terminal expansion
Frankfurt Airport currently serves up to ten wide-bodied aircraft simultaneously. The new A-Plus pier will increase this number by seven and alternatively provide enough space for processing several smaller aircraft. The intralogistics supplier BEUMER is currently constructing the new luggage conveyor system which is more than 7km long. The conveyor transport technology must not only be 100% available; it must also be capable of reliably taking the pieces of luggage to the correct destination in less than 45 minutes.
NORD DRIVESYSTEMS has installed over 1,700 geared motors in the extensive system with nearly 2,000 conveyor elements and over 100 junctions. Due to the new design and construction, smaller drives can be used at many points, leading to lower installation and operating costs. At the same time, drive sizes have been harmonised as far as possible and the number of models in use has been reduced in order to improve logistics and reduce the spares inventory, thereby improving cost-efficiency. Easy maintenance and repair is also ensured: the interchangeable drive units are attached with just a few screws and a single electrical connector, and can be replaced in the shortest possible time.
"For this project, NORD put together a team of sales, engineering, and logistics staff who were always available to us and quickly answered our concerns," says Klaus Ruhe, project manager at BEUMER. "The requirements concerning the logistics of the airport were responded to precisely and with flexibility."
Efficiently designed drive motors
The power performance of the motors varies between 0.55 and 3kW. All motors rated 0.75kW and higher are IE2 models which, for the conveyor application, offer a higher efficiency and use less energy than the previously often used drives in the EFF2 efficiency class drives (now classified as IE1). In order to implement the Ecodesign Directive, NORD uses very high-quality sheet metal with smaller losses and more active material in the stator. Additionally, the copper filling in the stator slots is increased and the winding scheme optimised.
Due to these construction changes, NORD’s IE2 motors offer a broader operating range, which is taken into consideration in the drive configuration. In some circumstances it is possible to install smaller motors than previously possible because of the greater power reserves. Depending on the motor size, some models can operate at up to 150% of the nominal power capacity, while maintaining high efficiency. When compared to their direct predecessor models, IE2-type motors offer higher start-up and breakdown torques and develop less waste heat.
Expertise in gearbox manufacturing
The gear units employed for speed adjustment in the facility are mostly SK9012.1 bevel gearboxes, supplemented by a number of SK372.1 helical gearboxes. About half of the drive units are equipped with brakes. NORD is not only a full-scale supplier of drive products and solutions, but also boasts a remarkable vertical range of manufacture including motors, inverters, and all gear parts – from casing and shafts to pinions and worms.
The housing construction follows the UNICASE principle introduced by NORD in 1981. With no welded seams, screw fittings, and sealed surfaces, the one-piece housing with integrated shaft bearings features maximum torsional strength and ensures excellent radial and axial load capacity. To improve accuracy and avoid wear and tear, all bearing surfaces are machined in one operation. Thus, the gear units not only achieve a longer lifespan than conventionally manufactured models, but are also particularly quiet due to smoother running.